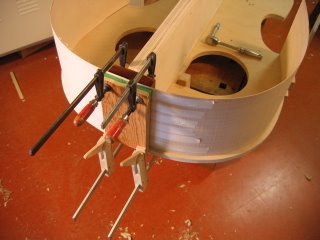
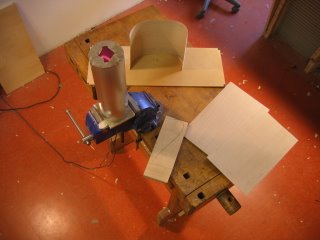
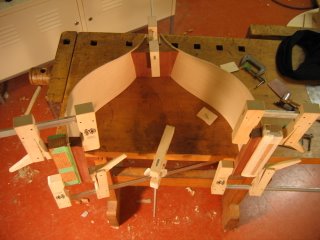
Ok, so I've been making my ribs and blocks and gluing them all together.
My ribs are a lamination of two layers of maple with a very thin layer of silk sandwiched between. The result is very strong, flexible and light 2mm ribs that resist cracking and are free to vibrate to add to the range of overtones of the finished bass -- good thing.
I once BOILED a sample of my ribs for an hour to see if they would de-laminate -- no way; I've hit them, smashed them, bent them, twisted them and otherwise tried get them to de-laminate, but no dice -- they're effectively one piece.
At this point, the corner blocks are glued to the lower and upper ribs with miters cut ready to fit the mitered centre bout ribs -- which I'm doing today.